Efficiency Redefined: Cutlery Manufacturing With Automatic Hydraulic Press
A quick overview of the topics covered in this article.
In making stainless steel tableware and utensils, combining precise technology and efficient automation is bringing in a new way of doing things. This article will explore the special features and advantages of hydraulic presses. Learn how these machines, when paired with automation, are changing how we make kitchen tools and cutlery, making the process more advanced and efficient.
Overview Of Hydraulic Press Machine Technology
The hydraulic press is super important for making stainless steel spoons/forks/knives. It has a frame, cylinder, workbench, hydraulic system, and electrical control system.
The way it works is based on Pascal’s law, which spreads pressure evenly using hydraulic oil in a closed system. When the hydraulic pump pushes, it sends oil into the cylinder, making the piston or slide move. This movement force goes to the metal material, letting us do things like shaping, stamping, and bending. So, the hydraulic press is a key player in making tableware efficiently.
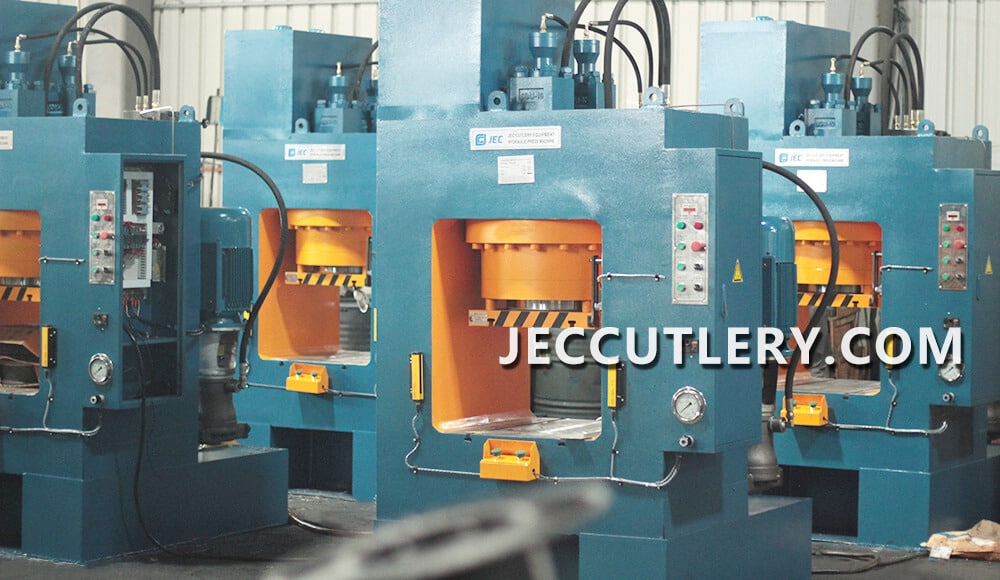
What Are The Advantages Of Different Structures Of H-type Hydraulic Presses?
The structure of a hydraulic press plays a big role in how well it makes tableware. Knowing the various structures of hydraulic presses is crucial to improving the cutlery production process.
JEC Cutlery Equipment offers two main types of H-frame hydraulic presses (200/300/500/700 Ton Hydraulic Machines): the upper oil tank hydraulic press and the lower oil tank hydraulic press. Each type has its own advantages for making tableware.
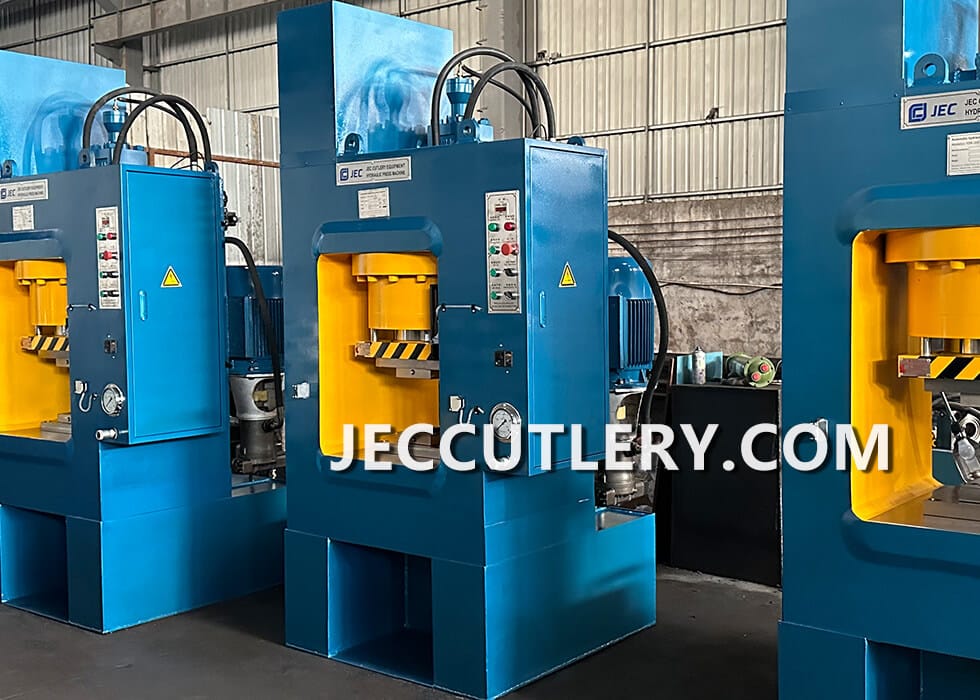
Upper oil tank hydraulic press: It adopts the design of an upper oil tank. Its main advantage is that the oil can flow back to the oil tank more easily, reducing the risk of leakage. This design helps keep the hydraulic system clean and improves productivity. In addition, the maintenance of the oil tank hydraulic press is more convenient, it is easier to achieve the lubrication effect and extend the life of the equipment.
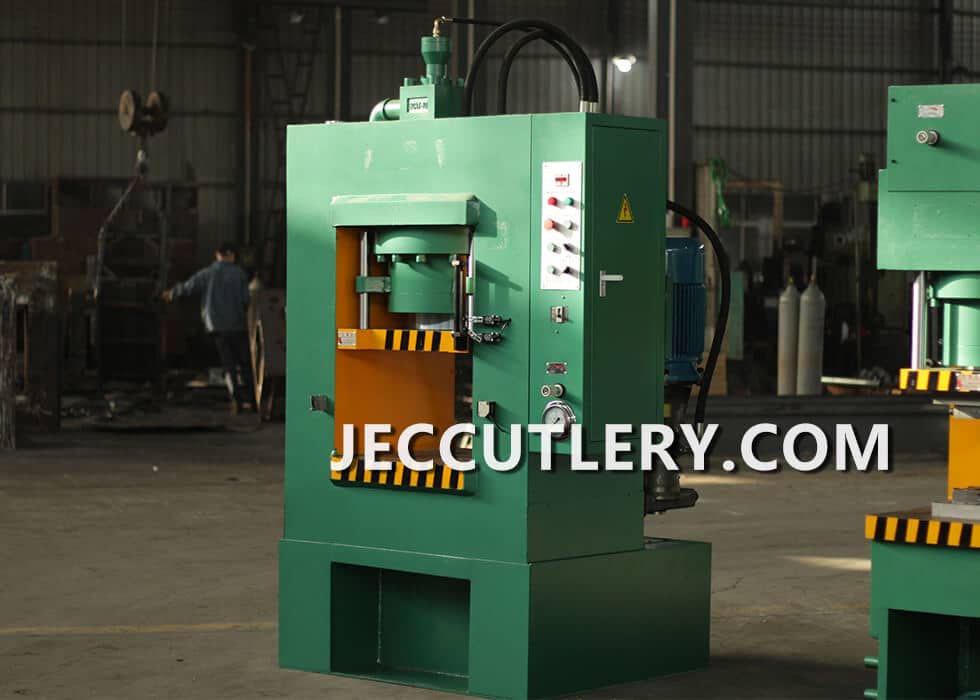
How Well Do Hydraulic Presses Work With Automation?
In the traditional production method, the operator is required to manually feed the raw materials into the machine and then perform stamping processing. This method is time-consuming and laborious, and may also be limited by the operator’s technical level, which can easily lead to product errors and waste of raw materials.
The introduction of the automatic feeder makes the production process more coherent. It can realize the automatic supply of raw materials, effectively shorten the production cycle, improve production efficiency, reduce labor costs and minimize material waste. Operators only need to monitor the operation of the production line, which reduces the labor intensity of workers and ensures the safety of operators.
Continuous Innovation Of JEC Automatic Hydraulic Presses
With the continuous development of society, people’s requirements for the quality of life are also increasing. Stainless steel tableware, as an environmentally friendly, durable and easy-to-clean cutlery material, has gradually become an indispensable part of people’s lives. Our company JEC is also constantly working hard to innovate. In 2024, we will make new upgrades on hydraulic presses and automatic machines, European-level hydraulic press automation systems.
- The system electrical component configuration is upgraded to big famous brands.
- Install a guide rail device on the automatic feeding machine.
- Added touch screen operation based on the original button operation.
Our purpose on the road of innovation is: quality wins the future! If you are interested in these machines, please feel free to contact us.
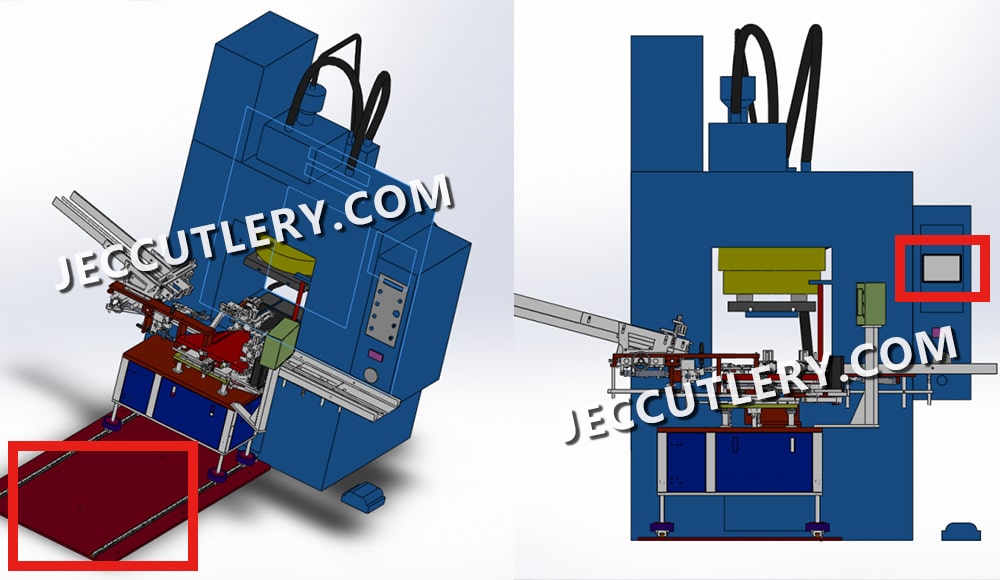
In conclusion, the marriage of hydraulic press work and automation stands as a testament to the ever-evolving landscape of cutlery manufacturing. This revolution not only elevates the efficiency and precision of the process but also paves the way for a future where technology and craftsmanship harmonize to create cutlery of unparalleled quality and design. As industries embrace this transformative wave, the artistry of cutlery making finds itself on a trajectory of continuous enhancement and innovation.
A quick overview of the topics covered in this article.